Детали дробеструйной машины. Часть 1
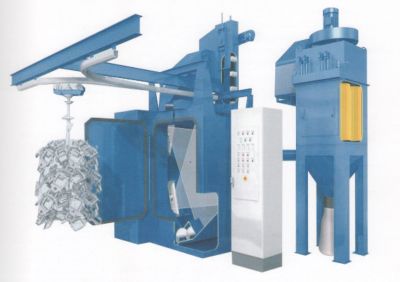
Дробеструйные машины состоят из 5 основных отделов: колесо, камера, элеватор, сепаратор и пылеулавливающая cистема. Очистка поверхности происходит при помощи циркулирующей в системе стальной дроби, которая нагнетается на поверхность литой части посредством колес. После удара о поверхность стальная дробь переносится в сепаратор как смесь частиц (пыль, окалина и т. д.) при помощи элеватора для отделения от нежелательных компонентов.
При помощи фильтрующей всасывающей системы сепаратора стальная дробь многократно используется для очистки, поэтому в камере происходит замкнутый цикл, а давление воздуха — непрерывно.
На чертеже показан основной принцип работы дробеструйной машины.
Процесс очистки
Процесс очистки состоит из слеующих шагов:
- Абразивный материал транспортируется для заполнения воронки, а затем нагнетается при помощи обоймы подшипника.
- Далее материал попадает на лопасти из проемов импеллера.
- Стальная дробь, которая попадает на лопасти, нагнетается на литую часть и производит очистку поверхности при ударе об нее.
- Частицы использованного абразивного материала (песок, стальная дробь и др.) направляются в конусообразный формованный бункер, а косозубое колесо перемещает смесь в бункер элеватора.
- Ковши элеватора забирают смесь из резервуара и транспортируют ее в сепаратор.
- Оставшиеся частицы, которые поступают из формованной решетки барабана, выпускаются из системы при помощи винта прямо из барабана. Те частицы, которые пропускаются решеткой, толкаются винтом и перемещаются в пневматический очищающий сепаратор.
- Маленькие частицы удаляются из смеси, которая стекает как завеса в пневматическом очищающем сепараторе, при помощи вакуума.
- Пыль перемещается в пылеуловитель, а песок транспортируется из системы.
- Очищенная стальная дробь возвращается обратно к колесу.
1. Турбина
Это самая важная часть дробеструйной системы, которая нагнетает абразивный материал на литую часть при установленной скорости и в указанном направлении. Обычно на турбинах расположено 6 и 8 лопастей, хотя это число может изменяться.
Части турбины:
1. Загрузочный желоб
2. Импеллер
3. Корпус
4. Фиксирующее устройство
5. Передвижная пластина
6. Лопасть колеса
7. Панель
Турбины являются главными частями машины, которые выполняют основные функции оборудования. Соответственно, их настройка и правильная эксплуатация важны для работоспособности всей системы.
1.1. Принцип работы турбины
- Стальная дробь поступает в импеллер из загрузочного желоба.
- Импеллер и лопасти вращаются с помощью двигателя непрерывно на высокой скорости, обойма подшипника не поворачивается.
- Стальная дробь в импеллере выходит из обоймы подшипника и попадает на вращающуюся лопасть.
- Лопасть на большой скорости нагнетает стальную дробь из проема, расположенного в нижней части колеса.
Схематическая иллюстрация участка перегрева
Для того, чтобы обеспечить высокий уровень функционирования, импеллер, подшипник и лопасти должны быть правильно настроены, иначе стальная дробь не будет нагнетаться в правильном направлении. При этом абразивный износ, который возникает у деталей, контактирующих с абразивным материалом, вызывает ошибку в настройках.
Колесо дробеструйной машины
Стальная дробь, которая попадает в импеллер, нагнетается после вращения между стержнями.
1.2. Виды турбин
Несмотря на то что для дробеструйных машин было разработано несколько видов лопастей колес, их принцип работы является таким же, как разъяснено выше. Различие может быть в пластинах, импеллерах и лопастях. Виды колесзависят от лопастей. Наиболее характерными используемыми являются: ровные, изогнутые и двусторонние лопасти.
1.2.1. Колесо с ровными лопастями
Колесо с ровными лопастями
Это наиболее часто используемый вид турбины. Самый простой вариант имеет диаметр 495 мм. Скорость продувки — 73 м/с при 2250 об/ч. Обычно функционирует на уровне 1035 кг/ч/кВт.
1.2.2. Турбина с изогнутыми лопастями
Колесо с изогнутыми лопастями
Данный вид разработан позже, чем тип колеса с ровными лопастями. При диаметре 457 мм, пока скорость конца лопасти равняется 50,2 м/с, стальная дробь достигает скорости 73 м/с. Векторный анализ изогнутой лопасти показан на рисунке 24. Турбины с изогнутыми лопастями, по сравнению с ровными лопастями, имеют следующие преимущества: меньший диаметр, меньший уровень шума и более низкую скорость вращения (то есть меньшее потребление электроэнергии). Ключевыми моменты, на которые стоит обращать внимания при выборе данных лопастей: песок должен тщательнее удаляться при помощи сепаратора, а стальная дробь не должна иметь высокий уровень твердости (на уровне между 55 и 65 HRc).
Графики для нескольких диаметров ровных лопастей:
A — 330 мм
В — 381 мм*
С — 495 мм
Е — 610 мм
Графики для нескольких диаметров изгонуых лопастей:
В — 330 мм*
D — 457 мм
F — 599 мм
* График В совпадает для ровных и изогнутых лопастей указанного размера
1.2.3. Турбина с двусторонними лопастями
Двусторонняя лопасть
Этот тип турбин обладает ровными и изогнутыми лопастями одновременно, был разработан для достижения более широкого участка перегрева. Разница между углами передней и задней частей составляет от 3 до 6 градусов, а загрузочный механизм расположен со стороны лопастей. Такие турбины используются при большом количестве лошадиных сил, в основном для систем подвесных типов. Время обработки существенно снижается. И, благодаря своей конструкции, он используется с колесами, которые крепятся только с одной стороны.
Разница в функционировании данных видов проиллюстрирована на рисунках ниже.
Разница между участками перегрева двусторонней и стандартной лопастей
2. Колесо
2.1. Факторы, влияющие на эффективность и производительность колес
Правильное функционирование колеса зависит от слудющих факторов:
- Интенсивность подачи абразива в колесо и скорость продувки абразива
- Смесь абразива
- Размер абразива
- Направление движение абразива, ширина и участок перегрева
- Состояние деталей колеса.
2.1.2. Интенсивность подачи абразива в колесо и его объем
Интенсивность подачи — скорость потока стальной дроби, при которой она возвращается обратно к колесу при помощи загрузочного желоба, уже после процесса очистки в сепараторе. Интенсивность подачи и производительность колеса и двигателя устанавливаются. Если система не приводится в движение, стальная дробь не может производить очистку.
Различные критерии, в зависимости от вида дробеструйной машины и ее характеристик, могут оказывать влияние на интенсивность подачи:
- мощность двигателя;
- размеры лопастей;
- скорость вращения колеса;
- количество лопастей колес.
Амперметр колеса
1) Контроль при помощи амперметра
Синхронизатор турбины показывает цикл работы колес при загрузке, исключая при этом время, когда оборудование было выключено. Современные дробеструйные машины имеют соответствующие измерительные устройства.
Но помимо синхронизатора нужно постоянно следить и за данными амперметра, который также показывает нагрузку двигателя.
По показаниям амперметра регулируется то количество абразивного материала, которое должно быть загружено в колесо. Устройство показывает уровень электрического тока, который потребляет двигатель. Пока рабочая нагрузка двигателя находится на максимуме во время обработки, будет выполняться самая быстрая и наиболее эффективная дробеструйная очистка. В зависимости от высокого или низкого значения необходимо выполнять разные настройки. Если система не функционирует на уровне производительности в 100%, амперметр показывает более низкую величину, в отличие от той, которая должна быть. В данном случае при считывании значения амперметра, оператор фиксирует наличие нарушения нормальной работы и пытается установить возможные проблемы.
Для каждого двигателя колеса есть точные значения ампер при полной нагрузке и без нее. Эти значения указаны в таблице ниже. Амперметр может не всегда показывать фактически используемый уровень тока, поэтому необходим и ручной контроль. Действительная максимальная нагрузка двигателей может быть считана с таблички, расположенной непосредственно на оборудовании.
Показатели двигателя | ||||
Мощность двигателя | 380 V | |||
кВт | л.с. | Io | Imax | Iu |
7,5 | 10 | 5,8 | 17 | 11,2 |
11 | 15 | 8,1 | 24,5 | 16,4 |
15 | 20 | 10,5 | 31 | 20,5 |
18 | 25 | 11,6 | 38 | 26,4 |
22 | 30 | 14 | 45 | 31 |
30 | 40 | 19,8 | 59 | 39,2 |
37 | 50 | 23 | 74 | 51 |
44 | 60 | 27 | 86 | 59 |
55 | 75 | 35 | 106 | 71 |
Использование на 1А меньше тока во время обработки дробью означает на 12 кг меньше количества дроби, которая нагнетается за 1 минуту.
Давайте рассмотрим 50 л.с. (37 кВт) двигатель, работающий при 50А. При использовании вышеуказанной таблицы показателей двигателя мы видим, что уровень тока, при котором работает данный двигатель при полной нагрузке, Imax = 74А, и без нагрузки, когда поток стальной дроби не попадает в колесо, Io = 23 А. А теперь вомпмользкемся формулой производительности.
В этом случае значение менее чем 74 - 50 = 24А будет получено из системы. При 380В и при 1А, колесо нагнетает только 12 кг стальной дроби. В нижеприведенной таблице указано значение количества дроби, приведенного в движение 8-лопастным колесом.
Количество стальной дроби,которое приводится в движение | ||
кВт | л.с. | кг/мин |
7,5 | 10 | 130 |
11,0 | 15 | 190 |
15,0 | 20 | 240 |
18,5 | 25 | 300 |
22,5 | 30 | 360 |
30,0 | 40 | 440 |
37,0 | 50 | 580 |
45,0 | 60 | 700 |
55,0 | 75 | 810 |
Если мы продолжим на основании данного примера, то будет нагнетаться на 24х12 = 288 кг стальной дроби меньше. Если этот двигатель будет работать при полной загрузке, то, как видно из таблицы, будет выбрасываться 580 кг стальной дроби. Если недостаточное количество дроби попадает в колесо, то использование стальной дроби высокого качества не имеет никакого смысла. Электродвигатели разработаны для работы при полной нагрузке и должны функционировать самым эффективным образом, иначе происходит увеличение эксплуатационных расходов.
2) Причины снижения значения ампер и пути решения данной проблемы
ПРОБЛЕМА 1: Абразив вообще не подается в колеса
Если количество абразива, которое нагнетается в колеса, возрастает, вслел за этим увеличится нагрузка двигателя и значение ампер.
Решение:
- проверьте, достаточно ли абразива в аккумулирующей воронке, которая загружает колеса;
- система перемещения абразива (конвейер) может работать не достаточно хорошо;
- могла возникнуть проблема в загрузочном желобе или загрузочном трубопроводе, что препятствует прохождению абразива;
- в системе элеватора могла возникнуть проблема с транспортирующей лентой или ковшом элеватора. Ковши также могут быть изношены.
ПРОБЛЕМА 2: Закупорка колеса избытком стальной дроби
Если количество стальной дроби, которое поступает в колесо, увеличится, значение ампер также увеличится, т.к. нагрузка двигателя возрастет. Если поток стальной дроби слишком большой, то она задерживается в импеллере и не может попасть в колеса. Это приводит к снижению потреблению тока и увеличению значения ампер. При нормальных условиях, для двигателя в 10 кВт должно быть значение в 20 ампер .
Решение:
- Канал абразива должен быть отрегулирован, загрузка не должна превышать пропускную способность колес. Когда обработка дробью останавливается, то заслонка на желобе подачи должна быть закрыта, чтобы абразив не оставался в колесах.
- Части колес периодически должны проверяться на наличие износа. Износ корпуса, лопастей и загрузочного желоба могут привести к избыточному уровню потока стальной дроби.
- Для колес, которые приводятся в движение при помощи ремня, его ослабление приводит к потерям производительности колеса, поэтому ремень всегда должен быть натянут. При возникновении данной проблемы двигатель колеса в свою очередь может быть разблокирован, и поступающая стальная дробь не может двигаться вперед и будет аккумулироваться в колесе, приводя к недостаточной загрузке лопастей. Значение ампер при этом снижается.
- Если что-то попадет в колесо, оно застрянет между импеллером и корпусом, приводя к деформации двигателя. Необходимо контролировать решето.
Недостаточная загрузка колес / предупреждение о форсированной подаче и блокировке потока
Используя простой тест, можно выяснить, где снижение значения ампер вызвано блокировкой потока, а где — форсированной подачей. Во время обработки дробью ее подача прекращается. Если значение ампер неожиданно снизилось, причиной снижения значения ампер является блокировка. Если значение значительно не изменилось, когда загрузка абразива остановилась, причиной низкого значения является недостаточная загрузка. Если значение ампер выше, чем должно быть, то причиной является избыточная загрузка.
2.1.3. Смесь абразивного материала
Самым важным фактором, который влияет на эффективность очистки, является смесь абразива. Смесь абразива должна всегда быть однородной, а маленькие и крупные гранулы должны быть вместе. Для этого нужно:
- каждую неделю проводить гранулометрический анализ;
- держать 2/3 бункера всегда заполненным;
- вводить добавочный материал в систему постепенно и часто;
- утечка абразива должна отслеживаться каждый день;
- сепаратор и система отсасывания воздуха должны контролироваться каждый день.
2.1.4. Размер абразива
Для того, чтобы удерживать уровень смеси в машине на стабильном уровне, добавление стальной дроби должно выполняться регулярно. Желаемое качество может быть достигнуто только таким образом. Если добавление стальной дроби выполняется только когда машина пустая, то эксплуатационная смесь остается при номинальной начальной величине. При нехватке в смеси стальной дроби среднего и маленького размеров и наличии только больших размеров поверхность получится неровная и грязная. Если эксплуатационная смесь достаточно высококачественная, недостаток стальной дроби большого размера, которая имеет большую энергию, приводит к недостаточной очистке, а время обработки становится значительно дольше. Еженедельное техническое обслуживание способствует проведению наиболее необходимых наладок. Время от времени анализ собранной пыли должен производиться так же, как и гранулометрический анализ эксплуатационной смеси. Эти анализы дают значительную информацию об эффективности очистки и об экономичности обработки.
2.1.5. Направление, ширина и участок перегрева абразива
В процессе очистки точная настройка направления потока стальной дроби является очень важным фактором эффективности. Участок перегрева — это зона наиболее интенсивного потока стальной дроби. Направление стальной дроби, нагнетающейся колесом, устанавливается при помощи регулировки устройства управления корпусом и определяется как ширина полосы, охватываемая струей распыляющего устройства. Без учета направления вращения колеса, его настройка направления по или против часовой стрелке производится с помощью устройства управления корпусом. Для того чтобы удостовериться, что установка устройства управления корпусом верна, контроль над шириной полосы, охватываемой струей нагнетающего устройства, должен выполняться регулярно, особенно каждый раз, когда какая-либо часть колеса перемещается. Процедура контроля ширины полосы, охватываемая струей нагнетающего устройства, представлена ниже.
Стальная платформа размещена в фиксированном положении в передней части колеса, которое необходимо отрегулировать. Очистка струей выполняется 5-10 секунд или более, и как только она заканчивается, маркируется ширина полосы, охватываемая струей нагнетающего устройства. Для многоколесных машин регулировка должна осуществляться для каждого колеса последовательно.
Сдвинуто влево | Сдвинуто вправо | Верно
Внимание! Для данного тестирования не должны использоваться такие материалы, как картон или фанера, так как они блокируют части машины, обеспечивающие поток материала. Фактически, ширина полосы, охватываемая струей нагнетающего устройства, расположена напротив проема корпуса и образует с ним угол приблизительно 170 градусов. Как можно увидеть из нижерасположенной диаграммы, наиболее применимая ширина полосы должна быть на 200 мм впереди от центра колеса.
Факторы, влияющие на направление дроби:
- перегрев внутренних частей колеса;
- неправильная настройка устройства управления корпусом;
- ослабление V-образных лент колеса;
- износ лопастей колеса;
- неустановившийся режим работы абразива.
Ширина полосы, охватываемая струей нагнетающего устройства
Темная область в середине характеризуется как «участок перегрева», на которой соударение стальной дроби является наиболее эффективным.
Правильно направленная концентрация стальной дроби является очень важным фактором, который стоит учитывать. Другими словами, нагнетающаяся дробь должна обнаруживать цель. Данные настройки выполняются подготовленным персоналом производителя машин. При помощи маркировки на поверхности обрабатываемого материала необходимо установить направление дроби.
Согласно положению установки некоторых импеллеров, нагнетание может производиться на более широкую или более узкую зону. Желобки на задней части импеллера (Изображение 2) расположены так, что длинные и короткие виды зон могут быть отрегулированы. Буквы S и L, расположенные между выемками, означают: S — для короткой и L — для длинной зон.
Колесо отрегулировано в позицию L | Колесо отрегулировано в позицию S
Нижерасположенный рисунок показывает изменения в эффективности ширины полосы, охватываемой струей нагнетающего устройства, при различных диаметрах и видах корпуса. В данных случаях, прямоугольных и трапециевидных корпусов.
Изменение ширины полосы, охватываемой струей нагнетающего устройства
А: 610мм — имеет прямоугольный проем с колесом с прямыми лопастями; 457мм - имеет трапециевидный проем с колесом с прямыми лопастями; 495мм — имеет прямоугольный проем с колесом с прямыми лопастями
В: 457мм — имеет прямоугольный проем с колесом с изогнутыми лопастями; 495мм — имеет прямоугольный проем с колесом с прямыми лопастями.
С: Импеллер специального дизайна (U.S. Patent 4, 164, 104)
Прямоугольные и трапециевидные проемы
Ширина полосы должна быть выбрана в зависимости от обрабатываемой части. Ниже на рисунке представлены две ширины полосы: А и В. Если выбрать А, то 43% удара стальной дроби приходится на деталь, а 53% — проходит мимо. Если область В выбрана как ширина полосы, то 71% удара стальной дроби приходится на деталь, а 29% — мимо. В данном примере необходимо выбрать тип В, что регулируется изменением типа или регулировок колеса.
Выбор ширины полосы в соответствии с литой частью
2.1.6. Состояние частей турбины
Почему изношенные части колеса должны быть заменены?
Изношенные и новые части колеса
Интенсивность подачи колеса регулируется в соответствии с дробеструйной машиной. Проблемы, которые возникают в колесе, являются причиной ухудшение данных настроек. При нормальных условиях проем импеллера регулируется таким образом, чтобы стальная дробь находилась в передней части лопасти, когда она попадает в проем. Таким образом, дробь попадает на лопасть равномерно, и та нагнетает дробь на деталь, которую необходимо очистить. Как можно видеть исходя из рисунка, стальная дробь расположена в обычном порядке и нагнетается на поверхность.
Правильно функционирующее колесо
Когда части изношены, корпус не может пропустить стальную дробь точно на лопасть. В зависимости от степени износа небольшое количество дроби попадает также и на обратную сторону лопасти. Это приводит к увеличению износа, главным образом, пластин и других частей, а количество дроби, которая нагнетается на деталь, увеличивается. Из-за того, что стальная дробь будет расположена как обычно, она будет сталкиваться друг с другом во время выпуска, что приведет к ее измельчению и будет являться причиной большего износа колеса.
Дисбаланс, изношенное колесо
Части, которые соприкасаются со стальной дробью, со временем изнашиваются, поэтому должны быть изготовлены с использованием износостойкого материала. Такими частями являются загрузочный желоб, предохранительные панели, импеллер, корпус, крепежный болт и лопасти. Кроме того, детали также не защищены и от динамической деформации, например, как при попадании гвоздя в колесо. Таким образом, материалы данных деталей должны быть устойчивы к износу и должны иметь ударную прочность. Так как эти две технические характеристики являются противоположными относительно друг друга, то необходимо достичь оптимальной комбинации.
Другим важным аспектом является то, что для предотвращения колебания лопастей в колесе (они должны быть такого же веса) должна быть выполнена балансировка.
Для замены частей колеса машина должна быть остановлена, что вызовет остановку производственного процесса, поэтому замена частей должна происходить настолько быстро, насколько это возможно. Дешевые и недолговечные части обходятся значительно дороже, по сравнению с частями хорошего качества, если мы будем рассматривать только затраты на техническое обслуживание. Во всем мире для производства этих деталей используется высоколегированный белый чугун, однако сейчас началось и изготовление с помощью порошковой металлургии.
Срок службы используемых частей колеса прямо пропорционален другим факторам. Например, если техническое обслуживание сепаратора не выполняется надлежащим образом и с определенной периодичностью, то не имеет значения, насколько хорошее качество у запчастей колеса; они быстро износятся. Если вы можете взять эти факторы под контроль, вы сами определите действительный срок службы частей колеса. Несмотря на то что стоимость замены частей колеса обычно составляет 15% от стоимости обработки дробью, частая замена, вызванная несоответствующим техническим обслуживанием и плохим качеством материалов, приводит к большим затратам.
Запчасти колеса
Рассматривая только цены запчастей, невозможно подсчитать точную стоимость обработки дробью. Срок службы и расчет должны вытекать из «стоимость = цена / жизненный цикл». Также к высоким издержкам компании может привести дополнительная остановка машины, поэтом износ запчастей колеса должен быть под постоянный конролем. При этом тип износа расскажет о том, какие проблемы есть в системе на данный момент. Например, если одна часть лопасти подверглась износу больше, чем другие стороны, то это означает, что дробь не нагнетается соответствующим образом, другими словами, лопасть находится в дисбалансе. При нормальных условиях каждая сторона лопасти изнашивается равномерно.3
Ключ к циклу с длительным сроком службы: правильное и регулярное техническое обслуживание
Чтобы продолжить чтение, перейдите в следующую часть.